Smart Hard Hats & Offshore Head Injury Protection
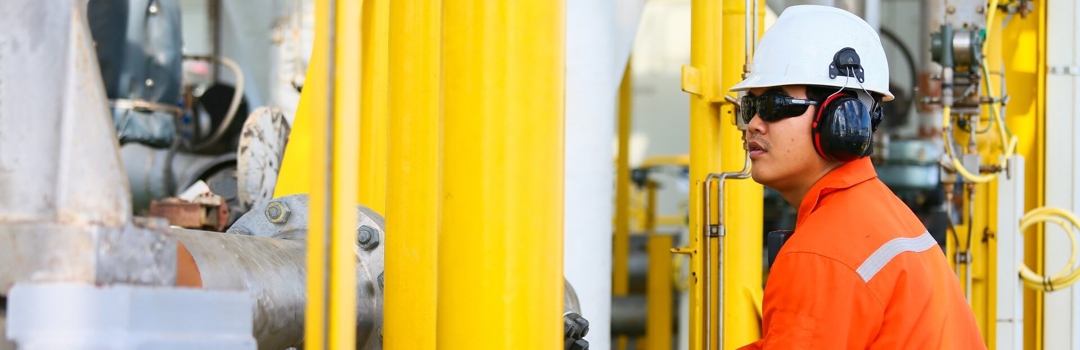
The sight of offshore workers wearing hard hats has become ubiquitous over the years. These important pieces of safety equipment protect the most crucial part of a worker's body from a range of unexpected accidents, and their significance is rooted in a rich history, reflecting the evolution of worker safety across different industries. Today, hard hats are being used in new ways to enhance safety offshore and in all worksites across the U.S. and worldwide.
The Legacy of the Hard Hat in Offshore Work
Before the 20th century, workers in hazardous environments typically relied on basic protection, donning simple leather caps or cloth hats. While these offered some shield against falling debris, their protection was admittedly minimal.
However, the landscape of worker protection experienced a significant shift in the early 1900s. A man named Edward Bullard, inspired by the steel combat “doughboy” helmet from World War I, pioneered the "hard-boiled hat" — a unique design crafted from steamed canvas, glue, and leather with a distinguishing black paint. With a suspension device added inside, this became the first commercially available device for head protection, now known as the hard hat.
As the mid-20th century approached, innovations in the petrochemical industry paved the way for new and different hard hat materials. The earlier canvas and leather designs began making way for thermoplastics, culminating in the 1950s when the Bullard Company rolled out helmets made of lightweight yet robust fiberglass.
This era also saw an uptick in offshore oil and gas exploration, after World War II. The unpredictable nature of offshore platforms, with their looming threats of heavy machinery and falling objects, necessitated the widespread adoption of hard hats, anchoring them as fundamental safety equipment.
Fast forward to the late 20th century and the dawn of the 21st, and the evolution of the hard hat showed no signs of slowing down. Newer, more resilient materials, particularly polycarbonate, started becoming the norm. The designs of these protective gears expanded to feature added functionalities like ventilation, face shields, earmuffs, and even integrated communication systems. At the same time, the importance of maintaining safety standards became paramount. Organizations such as the American National Standards Institute (ANSI) stepped in to set rigorous criteria, ensuring that today's hard hats offer optimal protection for workers, whether they're on land or venturing the depths offshore.
Protection Through the Ages
Since the 1970s, hard hats have been mandatory in the U.S. for certain situations, according to the Occupational Safety and Health Administration (OSHA). The specific requirements for hard hats can be found in the OSHA regulations under 29 CFR 1910.135(a)(1) and 29 CFR 1926.100(a). These sections state that protective helmets, commonly known as hard hats, must be worn when working in areas where there's a potential for injury to the head from falling objects. Additionally, hard hats are required where there's a risk of head exposure to electrical conductors that can contact the head.
Offshore, hard hats safeguard workers against:
- Falling Objects: Given the multilevel structure of many offshore platforms and the movement of equipment overhead, there's always a risk of objects falling. Hard hats provide a first line of defense against injuries from tools, equipment, or other materials that might drop from above.
- Blunt Force Trauma: Offshore workers often operate in tight spaces with heavy machinery and equipment. They can accidentally bump their heads against hard surfaces, machinery, or protruding objects. Hard hats help absorb and distribute the force of such impacts, reducing the risk of trauma.
- Hazardous Substances: While primarily designed for impact protection, hard hats can also protect workers from accidental splashes of corrosive chemicals or hot fluids.
- Electrical Shocks: Some hard hats are specifically designed to reduce the risk of electrical shocks from contact with exposed electrical conductors.
- Explosions and Blowouts: In rare cases, offshore platforms might experience blowouts or explosions. While hard hats cannot provide complete protection in such extreme scenarios, they can reduce the severity of injuries from flying debris or shrapnel.
- Environmental Factors: Hard hats can also offer some protection against environmental elements, such as the sun's UV rays, rain, or cold, ensuring that workers remain comfortable and can focus on their tasks.
- Fire and Heat: Some hard hats are made of materials that are flame-resistant and can protect workers from brief exposures to flames or excessive heat.
For decades, hard hats have been the first line of defense against unexpected accidents offshore, saving countless lives in the process. It stands to reason that their improvements would continue, not only in terms of the materials they’re made of, but the technology that can be used to make them more effective in preventing injuries and even stopping accidents from happening in the first place.
Smart Hard Hats: The Next Evolution in Offshore Safety
The integration of technology into hard hats, converting them into smart devices, may lead to significant advancements in offshore safety. According to a recent report, the objective is to transition from merely providing protection after accidents to proactive accident prevention.
Embedded smart hard hat technology may include:
- Temperature sensors for monitoring heat conditions.
- Humidity checkers to detect moisture levels, which might affect work quality.
- GPS modules for real-time worker tracking.
- SOS buttons to instantly alert safety teams during emergencies.
- Proximity sensors to keep workers safe from restricted zones.
These smart hard hat applications extend beyond individual safety. For instance, using GPS modules and proximity sensors, companies can monitor workers, ensuring they avoid dangerous or restricted areas. Should a worker approach a potential hazard, the hard hat's alert system can provide real-time warnings. In case of severe accidents, the embedded panic buttons and GPS functionalities can dramatically reduce response times, potentially saving lives.
One useful application involving smart hard hats became apparent during the height of the coronavirus pandemic. At a 2,200-person construction site in Europe, a company used a worker’s smart hard hat location-tracking abilities to map his movements after he became ill with COVID-19. They were able to identify all workers he came in contact with and areas that might need disinfecting, helping to reduce the likelihood of widespread illness among site workers.
Balancing Safety & Productivity in the Age of Smart Hard Hats
It’s estimated that the smart hard hat industry will be worth about $1.2 billion by 2025. While they promise enhanced safety measures, these hats also offer companies a means to monitor worker productivity. But this comes with its set of challenges. While tracking efficiency metrics, it's crucial not to neglect worker well-being. Overemphasis on productivity might overshadow factors like exhaustion.
Thus, as we look to a future dominated by smart hard hats, striking the right balance between safety and analytics becomes paramount.